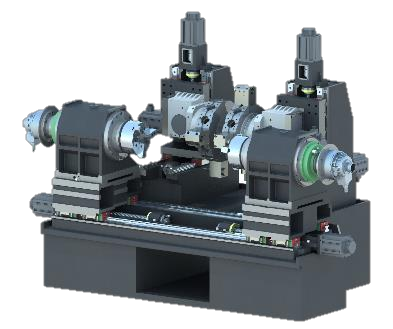
First of all, for the precision control of CNC drilling and milling centers, the most basic thing is to ensure the stability and rigidity of the machine tool structure. The stability of machine tools can be achieved by strengthening the basic support of the machine tool and using high-rigidity materials and structural design. The improvement of rigidity can be achieved by increasing the beams, bed and other structures of the machine tool. This can reduce the vibration and deformation of the machine tool during movement, thereby improving processing accuracy.
Secondly, the accuracy of the CNC drilling and milling center is also closely related to the accuracy of the guide rail. The guide rail is the core component of the machine tool, which directly affects the accuracy and stability of processing. Therefore, before using a CNC drilling and milling center, the guide rails should be regularly inspected and maintained to maintain their surface finish, lubrication status and geometric accuracy. At the same time, the accuracy of the guide rail can also be adjusted according to actual needs to ensure the accuracy requirements of processing.
Third, the selection and grinding of cutting tools in CNC drilling and milling centers also have an important impact on machining accuracy. The quality of the tool is directly related to the smoothness and dimensional accuracy of the machined surface. Therefore, when using a CNC drilling and milling center for processing, you should choose appropriate tools, and check and replace the tools regularly. Also, attention needs to be paid to the correct grinding and adjustment of the cutting tools to ensure the sharpness of the cutting edge and the accuracy of the geometry.
Finally, the accuracy adjustment method of CNC drilling and milling centers includes the adjustment of machine tool parameters and the optimization of processing procedures. The adjustment of machine tool parameters mainly involves the calibration and error compensation of motion axes. By adjusting the machine tool's motion axis based on actual measurement results, errors can be eliminated and machining accuracy improved. The optimization of machining programs mainly reduces machining errors and vibration through reasonable cutting parameters and path planning. Machining accuracy can be improved by optimizing cutting speed, feed speed, cutting depth and other parameters.
In short, the precision control and adjustment methods of CNC drilling and milling centers are multi-faceted, including the stability and rigidity of the machine tool structure, the accuracy of the guide rails, the selection and grinding of tools, the adjustment of machine tool parameters and the optimization of processing procedures, etc. Only by comprehensively considering and implementing these methods can the high-precision machining effect of the CNC drilling and milling center be ensured. Therefore, when using a CNC drilling and milling center for processing, these methods should be strictly followed to operate and adjust to improve processing quality and efficiency.