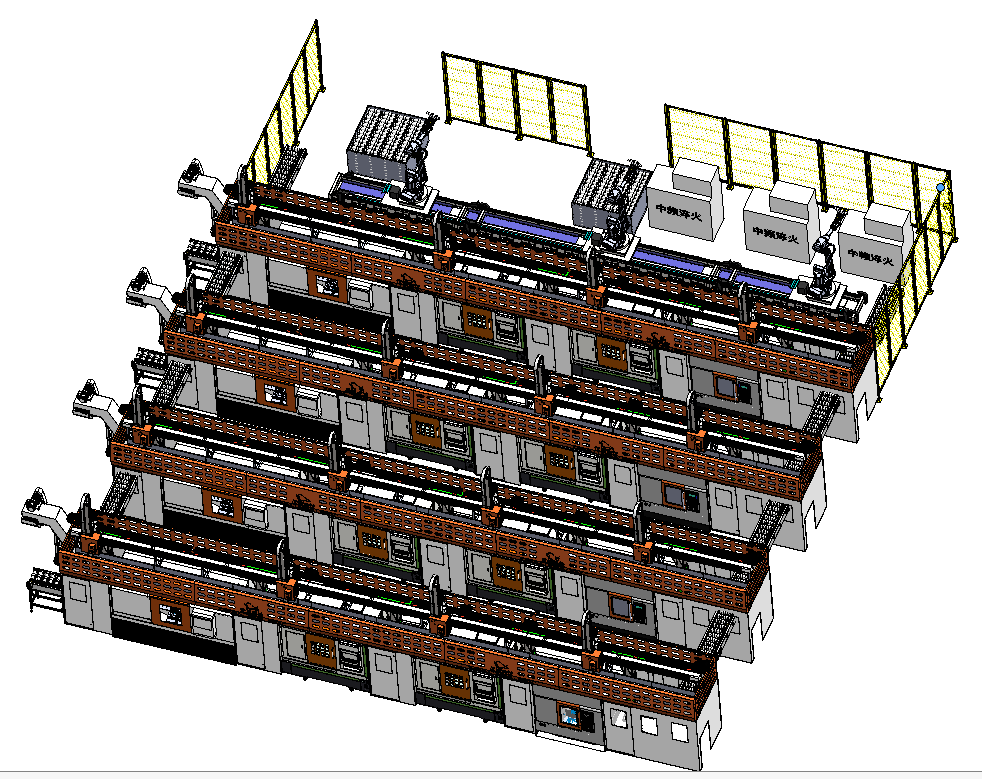
Unit Automatic Line
The automatic line consists of three parts
(1) Op10 one pull two truss automation unit (2) 0P20 punch automation unit (3) op30 one drag one truss automation unit
Loading and unloading instructions:
1. in order to connect with the precision forging workshop, the feeding device adopts tray type automatic silo.
2. At the end of the processing, the material is unloaded to the string bar unloader, which is manually removed and connected with the finishing area.
The precision machining industry mostly produces products with multiple specifications but in small quantities. Traditional machining processes involve manual loading and unloading, tool changes, and fixture adjustments, leading to significant wastage of production and processing time.
To address these issues, flexible machining production lines have emerged as a perfect solution. By employing multiple CNC machine tools, these production lines can carry out various different processes simultaneously. The modular automatic line, also known as automatic loading and unloading robots, can be used with standalone equipment or combined to form multiple units for online production. The automatic loading and unloading robots work closely with CNC machine tools to create unmanned machining systems. The robotic gantry can be installed independently on the ground or fixed on the machine tool, simplifying the mechanical structure and control system, ensuring stable operation and easy maintenance. Currently, gantry robots are applied in automating the loading and unloading processes of CNC lathes, machining centers, grinders, gear cutting machines, and cleaning machines.
The automation structure of machining includes a gantry and a robotic arm placed on the gantry. The gantry consists of several gantry support structures with a crossbeam for mounting the robotic arm. The automatic loading and unloading robot, a two-degree-of-freedom robotic arm, includes a horizontal motion component mounted on the crossbeam and a vertical motion component installed vertically on the horizontal motion component. At the bottom of the vertical motion component is a three-jaw gripper. The horizontal and vertical motion components consist of gears and racks for transmission, with the gears and racks designed with helical teeth for efficient engagement. This design allows the automatic loading and unloading robot to effectively carry out the loading and unloading tasks for processing workpieces.
In conclusion, the integration of automation technology in machining processes has significantly enhanced efficiency, productivity, and precision. By implementing flexible production lines and robotic systems, manufacturers can optimize their operations and meet the demands of producing varied products with minimal wastage.
Flexible machining production lines have been installed at the customer's factory.