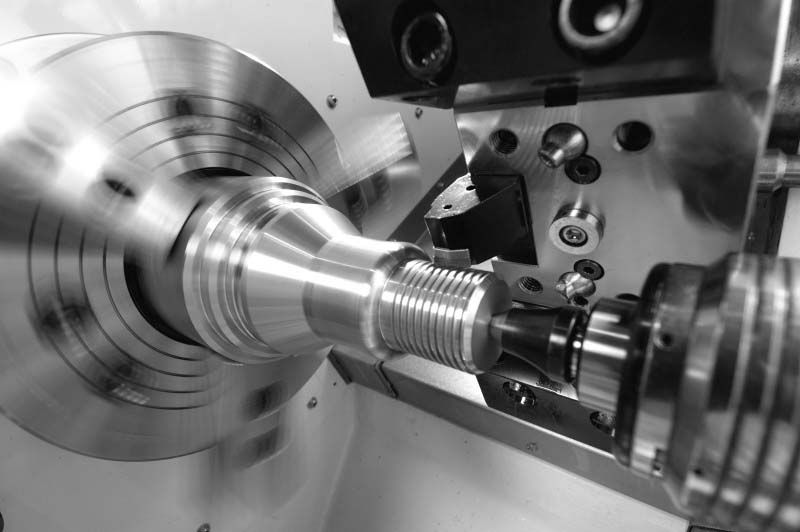
1. The tool does not return to zero after the program operation is completed.
This is usually a control system failure. When the tool is feeding or processing, the stepper motor operates at a low speed, and when the program returns to the zero point, it is required to return quickly. The stepper motor operates at high speed and uses a high-voltage drive power supply to increase the output torque. There is a switching transistor that controls the output of the high-voltage drive power supply. When the switch transistor is damaged, the high-voltage power supply cannot be turned on when returning to zero at high speed, and the stepper motor cannot output torque, causing the tool to not return to zero. This can be eliminated by replacing the switching transistor.
2. The workbench suddenly stopped during operation
This phenomenon is usually caused by mechanical failure, but it may also be caused by a failure of the control system. At this time, you can return the workbench to the origin and restart the processing program. If the workbench always stops working at a certain position, it may be that a certain part of the transmission system is damaged, deformed, or stuck by foreign objects.
First cut off the power, and then check whether the gap between the nut and the screw or whether the slide strip is too tight, whether there are foreign objects in the ball guide groove of the ball screw, whether the screw is bent or deformed, and whether the flexible gear in the stepper motor reducer is loose. Or foreign objects are stuck, etc.
3. The size of the processed workpiece varies greatly.
One possibility is that the screw or screw nut is loosely connected to the inclined bed CNC lathe. There is no cutting resistance during idling, and the slide plate operates normally. During processing, due to the increase in cutting resistance, the connection between the screw or nut and the lathe becomes loose, causing the workpiece to be processed to drift in size. Tighten the connecting part and the problem can be eliminated.
Another possibility is the formation of an electric tool holder. If the tool holder cannot be automatically locked after changing the tool, and the tool deviates from the processing point during cutting, the above phenomenon will also occur. At this time, you should check the tool holder locking device and the tool holder control box.
4. Processing programs are often lost
If the machining program is lost after the control system is powered off, and the machining program is re-entered after the inclined bed CNC lathe is powered on, and the machine tool can process normally, it may be that the backup battery voltage is reduced or disconnected, causing the machining program in the data memory to be interrupted on the machine tool. Unable to hold on after charging and lost. Just replace the backup battery.
If the processing program is often partially or completely lost during the processing, it may be a data memory failure. In this case, the off-chip data memory or the microcontroller itself can be replaced.